I support a charity that is working effectively on
stopping Slavery. Whilst most of you reading my article will probably have a
very comfortable life, there are many in the world suffering slavery. Your
donation to
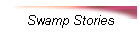
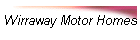
GT40E Build History.

Build History 3
From visiting of Roaring Forties in Melbourne, at the F1 that was not (COVID). To the first week of working on the car.
Installing batteries, Loads of wiring, Making Dashboard and so much more.
Build History 3 from Dec 4 2023
Note the sequence of the build on this web page read from the bottom up. (The most recent event is at the top of the page)
December 5 To March 28 Week 102. Most importantly the car had its first drive, this was after we found the reason why the Tesla was not working.
The other things done over the period were: MoTeC Dash updated, Speedo working, Programming of hand break, Jack leaks fixed, Wing mirror dimmer, Installed CV, Roll pinned doors, Air flow ducts for rear batteries, Remote drive created but not installed, BMS replaced, Rewiring of rear PDM and reallocating pins, Double microswitch for hand break, guards under the car to protect wiring, Trolly made, 4 batteries replaced, Cameras aligned.






The MoTeC dash has the plenty of room to display information, the photo above shows Page 1 of the dash. The left side where the parking cameras are displayed, The right other information (The item is not displayed if not called). Doors open or closed, Seat belts not on, Break Fluid low, Water Pump not running, Park break on in Neutral, Auto hand break selected, Hand break on, Gear that is selected D N R, Motor Temperature, being invertor and Rotor, Indicators, Head lights right and left dipped or not (They are independent) Driving Lights, Power in 300v battery, Outside Air Temperature. Others self explanatory.
I had some leaks on the Jacks, one came from one solenoid that was installed the wrong way round, one hose leaked, and once fixed it would hold full pressure.
Glenn from Auto Sports Electronics programmed the traditional Speedo to obtain information from both the GPS and Tesla.
One of my wing mirrors, Audi, is able to dim and Chris who has helped me with Arduino programmed the mirrir to dim when the Ambient light sensor indicated that it is darker than another light sensor that faced rearwards. In other words if it is dark and there is a bright light behind the wing mirror dims.
When the Doors are aligned with the bodywork, the bolts that locate the doors are tightened as much as possible. Unfortunately this will not stop them moving when doors are lent on. So having adjusted the doors so that they fitted just right I drilled and drove 2 roll pins top and bottom each to prevent any more movement. Don't Drill until you are 100% aligned.
I installed an aluminium plate under the car with air scoops that allows air to flow through the rear battery boxes, for cooling. Within the air flow there is a filter to prevent dirt penetrating the battery box.
During the initial wiring of the car, specifically to the rear PBM, some of the wires ended up being too short, thus making it hard to re-pin A or B plugs. In addition the direction of the wiring, to the front or rear of the car from that PDM were somewhat random. So I stripped all the wires out of the PDM. put a 30 pin plug in an aluminium wall coming into the sill below the PDM. Then rewired the whole lot, thus cleaning up both the PDM's programming and the cabling. Somehow I had 3 wires left over. And yet the car works fine!!
From past experience with linier actuators, I use one for the hand break, They tend to tear themselves to pieces when not programmed to stop before the stress gets too high. I have an actuator operating the hand break. This is stopped by a micro cam operated switch. My concern was that if the microswitch failed so would the actuator and so the hand break. I therefor installed a second magnetic microswitch, with either stopping the actuator moving. If either failed the break would still work, but a message would inform the driver that one microswitch failed.
The car has a 360° camera system, this having been installed some time ago. I had the opportunity to align the computer to merge all four cameras so as to make one (Drone) view. I little bit of playing about was required for the GT40, as its width and length are hardly standard.
A lot of time was spent building glass fibre protective guards that go under the car, inside the sills and in front of the rear wheels, these are yet to be installed, so see next post. In addition I have virtually finished the Remote controller, that will allow me to drive the car in or out of a parking space, when I am not in the car. Again details next post.
Prior to Christmas, Johannas from Openinvertor came online to look at the Tesla, and despite being in Germany he was able to pick up a few errors in the setup. We did continue to have some problems with the motor not running correctly. It would run on the throttle, but as soon as it got some revs would stop. In Mid March Johannas came online again and whilst I was trying to run the car he was looking at the Tesla's outputs. As soon as he mentioned that the Drive was switching off I knew the issue. I had a bit of code designed to stop Drive or Reverse selection when the car was moving. So I could not go D to R when other than stopped. The problem was it deselected Drive as soon as the car moved. This took a minute to fix and 4 months of searching was resolved.
Next I had the car insured to drive and on the 25th of March and despite struggling from food poisoning I drove the car round the block. A few issues were found and fixed, including the need to raise the car from 100mm clearance to 120 front 130 rear.
December 4, Week 88, Continual problems getting the Tesla to work, Wheel alignment, Clean some of body work, Refit cameras, Farting, Windscreen, Clean up MoTeC programming, OAT installed, Air Vent, Handbrake tune, Didgeridoo support, Side vent grills, Running 2 Teslas.



There has been a consistent issue with the Tesla. Firstly there has been an issue that when the 300 volts is wired up the motor starts to run, even when there is no throttle input. The other issue being that we are not getting understandable outputs into the Canbus. We were concerned that there was an issue with my Tesla motor.
To prove this one way or another, we bought Tim's identical Tesla next to mine, together with his battery pack, throttle and wiring harness. We ran his unit, it ran fine. We then connected his harness to my motor and it ran fine. we then gradually exchanged his components with my car's and things worked fine until the 300 volts was exchanged. At this point as soon as the forward or reverse was selected the Tesla turned, with no throttle, not good. We will shortly be connecting with Open invertor to see if they can fix the problem.
The MoTeC has been programmed to a point where it is virtually full to capacity, however I know that there will be more data to be entered. So I have spent time polishing the system. I have had experience doing this many years ago with my first computer, that had 1.6k memory. I changed a line of code that asked a question with a "Yes/No" I changed it to "Y/N" and could get another line of code.
The MoTeC is not like your average computer that you can keep programming to your hearts content.
The distance sensors have been programmed into the MoTeC so that warning noises will be made when I get too close to objects, or even lights switched on to light up the object.
I decided that Error noises should be farting noises. I since found that this is an option in Tesla cars.
I did have an issue with the cameras but they are now fixed. I found, after having spent money on a new set of cameras, that the wire shield actually carried a 12v supply, big expense fix.
The wheel alignment has been done, at least to a point where the car I hope will be drivable.
The car went to Rockingham to have its front windscreen fitted. Although this has been done so that it can be removed, when I prepare the car for paint, it will be ok to drive.
An OAT was fitted (Outside Air Temperature) was fitted with the output on the dash.
Eyelashes were fitted to the car, These stop the door lifting when the car is at speed, but need to have a very small gap to allow the door to shut without scraping the paint work. To get the eyelash in, hopefully, in the right position. I used 5 min Araldite to glue the eyelash in position. Broke the 5 min glue. I then drilled and screwed in place with the use of rivnuts. Once in place 24 hour Araldite was used to permanently secure. Then body filler to clean up.
One thing I do not like to see is NACA / Air ducts that are blocked off. Either use them or get rid of them. There is a large duct at the top of the bonnet. I have put a grill in place where it was and made an air vent that opens and closes, with the use of an Arduino that operates a servo, thanks to Chris.
One of the issues with a GT40 is that there is little room for luggage when going away for more than a tooth brush and jocks. (Underwear for non Aussies.) I have plans for that later but where do I store my Didgeridoo when I go for my lessons. I have an aluminium barrier to the left of the central tunnel. I built a carbon barrier on the right, guarding the pedals. This allows me to slip my Didge in place.
August 27, Week 75. A Long time between last update, Jack Solenoids working, Distance sensors installed, MoTeC PDM updated, Bonnet hinged Charger plug installed, but not charging, Locks on boot, Aluminium panels around footwell, Jenny's Mirror finished, Fresh air vent started, Perspex fitted, Fuses for bottom batteries, BMS wiring, Kevlar sill, Indicator cancelling, Moved the car, Perfecting programming, Right beam dip, Program 8 button module, Seat belt warning, Wing Mirror folding and additional wiring, Cameras not working.



So that I can move the car around in the garage, I have had pneumatic jacks installed by Roaring Forties. The solenoids are now installed and programmed within the MoTeC. So that a press of a button lifts the car, and a trolly can be pushed under, F1 style. It all works nicely apart from some leeks. To be fixed.
Distance sensors have been installed around the car, three at the front and 4 on the back. As sensors do not give a simple voltage change as an obstacle gets closer it was necessary to have some help. I know a tiny bit about Arduinos but only enough to know that one would be the solution. I managed to track down Chris who programs the simulators an the local RAAF aerodrome. He built the hardware and little fiddling we had it working, but as yet not showing properly on the MoTeC display.
As the build progressed, I began to push the MoTeC to its limits. My aim is to have the car have all the functionality of a modern road car, including all the warnings, cameras, distance sensors and so on, in addition to being able to run an electric motor. Originally, I had a PDM 30 in the front and a 15 in the back, but changed this to a 30 to increase functionality.



The Main Battery charger has been installed but we are having problems trying to get the CanBus talking. Unfortunately, this prevents us from running the motor. We did have an issue when finishing installing all of the BMS monitors, in that a fuse blew in the bottom battery box. These fuses were only installed in case of an unforeseen short, but we got one! So a days job to remove the top box, even though all connections are plugged in, top to bottom. 7-amp plugs were installed in the bottom box and a new bank of fuses installed externally with 3-Amp fuses, that hopefully would blow first. We went away for a week but when we got home the delivered fuse boxes had been taken from the mailbox. So another delay waiting for replacements.
When at a rally I saw a GT40 with rather nice boot lock, In Australia boots that open backward have to have a second locking mechanism, as with bonnets.


A few Aluminium panels have been installed in the footwell surrounding the Airconditioning compressor. The BMS monitor has been installed, together with Jenny’s vanity mirror. Full details are best seen on the video
The Headlight, indicator and side windows were shaped and attached, although they were then removed, to save damage.
The glass fibre sills were given a Kevlar layer to increase their strength, as they are the last protection against some of the 300 Volt batteries.
The indicators are now programmed so that the steering wheel will cancel them, as with a standard road car. This is done through the MoTeC and a steering angle sensor.
Other programming of the MoTeC includes a system that is copied from my Lexus, that will dip the right headlight, independently of the left. (In Australia we are Right hand drive.) I love this as it allows on coming traffic to see a dipped beam. But full beam will still light up the left gutter.
The Grayhill 8 button console has been programmed, and stickers added, thanks to my friends at Morley Sign Works. These operate:-
The Car jack up and down
Wing Mirror heater and Fold / Unfold
Engine sound off / on
Garage Door
Camera Drone View
Fresh air ventilation.



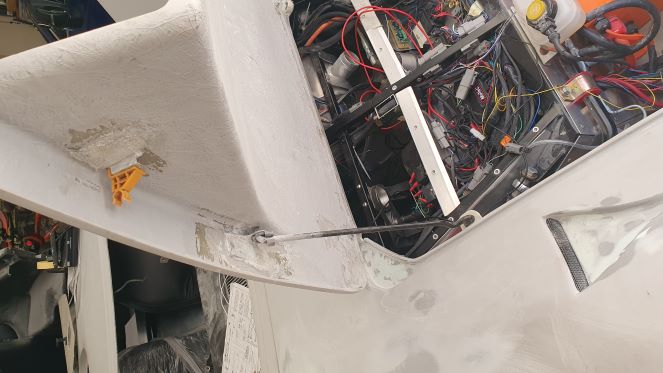
I purchased from Cete Automotive GmbH their Sound Booster, that I hope will do the job making the car, although being electrical, sound like a GT40. With the help of my friend Sid and a local exhaust supplier, now retiring, make an exhaust pipe for me.
The cameras have all been installed but are not working.
Finally I modified the bonnet so that it was hinged, Lotus Hinges from Vintage parts in the UK. Like so many jobs that I have done on the car, I had to do it twice. Having measured up the hinge’s position I found that it was about 3mm out, due to the hinges design, so the holes had to be filled and glassed and a refit. A bonnet prop was purchased and fitted prom a little Citron.
Lorem ipsum dolor sit amet
March 31 2023, Week 58. BMS Installed, Speaker Boxes made and Installed, Water Pump, Modified Battery Boxes, Hand Break, Car Weight.






Good progress this month. The batteries BMS (Battery Management System) is finally installed and checked. The BMS has 8 modules that measure the voltage difference between adjacent pairs of batteries. I had these all wired up. A check that all the batteries were wired in the correct order and had a good connectior was so much easier to check this with some help, one checking the connection and cumulative voltage, the other person filling out the spread sheet that records the battery location, its BMS monitor and connection. We have not got the motor running yet but hopefully this will be fixed this week.he other job was building the speaker boxes, that I have chosen to install behind the door hinges. The boxes are made of a glass foam glass sandwitch.
I purchased a Lingenfelter water pump, as per the pump used in the S Tesla. The pump is naturally electric with four connections. 12v and Earth and an additional 2 wires managing the PWM (Pulse Width Modulator). This manages the water flow, that MoTeC will manage. One issue we had was trying to get the pump to work, this being that it will not work without water being in the pump.
Speaker boxes were made out of Glass / foam / glass sandwhich. The holes were drilled in the aluminium to let the sound out. I made a jig using Illustrator this was printed onto a sheet of paper and holes made in the paper to mark the drill points with a felt tip.
As I did not use the best orange paint for the battery boxes I am getting them resprayed.
The other job was insalling a small knurled wheel, made from one of the brass battery connectors. I bougt a knurling tool for less than the cost of an enginere doing the job for me. The knurled knob adjusts a microswitch that controles the electronic hand break's limit. I chose to adjust it manually rather than try to develope an automatic system.
I weighed the car 1,450 Kg with I think a reasonable CofG location. New springs have been ordered to manage the heavier but reasonable weight.
The MoTeC has been programmed to a point where it is virtually full to capacity, however I know that there will be more data to be entered. So I have spent time polishing the system. I have had experience doing this many years ago with my first computer, that had 1.6k memory. I changed a line of code that asked a question with a "Yes/No" I changed it to "Y/N" and could get another line of code. The MoTeC is not like your average computer that you can keep programming to your hearts content.
The distance sensors have been programmed into the MoTeC so that warning noises will be made when I get too close to objects, or even lights switched on to light up the object.
I decided that Error noises should be farting noises. I since found that this is an option in Tesla cars.
I did have an issue with the cameras but they are now fixed. I found, after having spent money on a new set of cameras, that the wire shield actually carried a 12v supply, big expense fix.
The wheel alignment has been done, at least to a point where the car I hope will be drivable.
The car went to Rockingham to have its front windscreen fitted. Although this has been done so that it can be removed, when I prepare the car for paint, it will be ok to drive.
An OAT was fitted (Outside Air Temperature) was fitted with the output on the dash.
Eyelashes were fitted to the car, These stop the door lifting when the car is at speed, but need to have a very small gap to allow the door to shut without scraping the paint work. To get the eyelash in, hopefully, in the right position. I used 5 min Araldite to glue the eyelash in position. Broke the 5 min glue. I then drilled and screwed in place with the use of rivnuts. Once in place 24 hour Araldite was used to permanently secure. Then body filler to clean up.
One thing I do not like to see is NACA / Air ducts that are blocked off. Either use them or get rid of them. There is a large duct at the top of the bonnet. I have put a grill in place where it was and made an air vent that opens and closes, with the use of an Arduino that operates a servo, thanks to Chris.
One of the issues with a GT40 is that there is little room for luggage when going away for more than a tooth brush and jocks. (Underwear for non Aussies.) I have plans for that later but where do I store my Didgeridoo when I go for my lessons. I have an aluminium barrier to the left of the central tunnel. I built a carbon barrier on the right, guarding the pedals. This allows me to slip my Didge in place.
February 28 2023 Week 54. Modify Battery Beams, Install Side Batteries, Rewire BMS Monitor, Install BMS Monitors.
Something of a
frustrating month. I have certainly learnt that when you build a car that nobody
else has made before, i.e. a Tesla powered GT40 there is a lot to learn and
there is often two steps forward and one back. Sometimes due to silly errors.
In this month's case having installed the rear batteries I realised that on the
top of each battery there is a release valve. My problem was that the beams
that hold the batteries down cover these valves, thus making them inoperative.
So I disassembled the batteries, drilled the beams on the underside, and cut
the rubber over the release valve. Over a week to get back on track. Anyway,
now I have all the batteries installed, not only at the back but also under the
sills and the front. Now I am installing the BMS modules. With 74 wires it is
certainly worth while keeping a comprehensive spread sheet that tracks. Which
box and battery, plug and pin for each cable.
Another job was wiring the two 24 pin plugs that link the Top and Bottom
battery box. As I used concentric twisting, I found that to use many colours
made life much easier.
Well it appears a short report for a month of work, but much is learning.
January 30 2023 Week 50. BMS Wiring Bottem Battery Box, Add Top Battery
Box, Coffee Cup Holder with BMS Monitor, Broke Table & Build Trolly.
will help stop this
trade.
If you live in Western Australia you can support us by donating your
Containers for Change to C104 81 669 or deliver to Mount Hawthorn Baptist
Church's white bins.
May 14 2023 Week 65. Tesla talking to MoTeC, Cameras installed and talking to MoTeC. Distance sensors arrive and indicate some work in the future, Radiator grill installed, NACA ducts modified.With six weeks of work done since the last post, it looks as if little has been done, I think that this is what happens as the project progresses. The major progress is that we have the Tesla talking to the MoTeC. This is done with the installation of the Openinvertor power board, that replaces the Tesla board. You can not communicate with the Tesla. With the help from Tim at EVWorks and Glen from Autosport Electronics communication began. I then started to fill in the communication channels into the MoTeC.
In addition I installed the cameras supplied by Surround Monitoring System, these are now able to display on the MoTeC, mounted into the grill. I also received delivery of the distance sensors, but as these do not output a resistance or voltage for the MoTeC to understand. I will have to put my very limited Arduino skills to use. See the future.
A few other jobs have included installing the radiator grill, made from security door mesh. In addition as I hate to see air ducts of any kind blanked off, I have opened up the NACA ducts and put mesh in them. I have since noted that the centre bonnet duct is a little too deep, so some modification will be required there in the future.



Mounty Church